GMP stands for Good Manufacturing Practice and is a quality control system that makes sure that every pharmaceutical product is adequately tested and dosed for optimal effectiveness. GMP also controls the quality of food, diagnostics, ingredients in drugs and food, pharmaceutical products and devices used in medicine. Thus, GMP makes sure that a company follows a set of rules and regulations, producing something that meets all the necessary quality requirements.
Requirements of GMP
First of all, manufacturing processes need to be strictly defined and well controlled, ensuring that any product is made in accordance with predefined specifications. Secondly, during this control, if any changes or alternations affect the product, it should be analyzed and checked for quality. Should the product lose quality due to these alterations, it should be discarded.
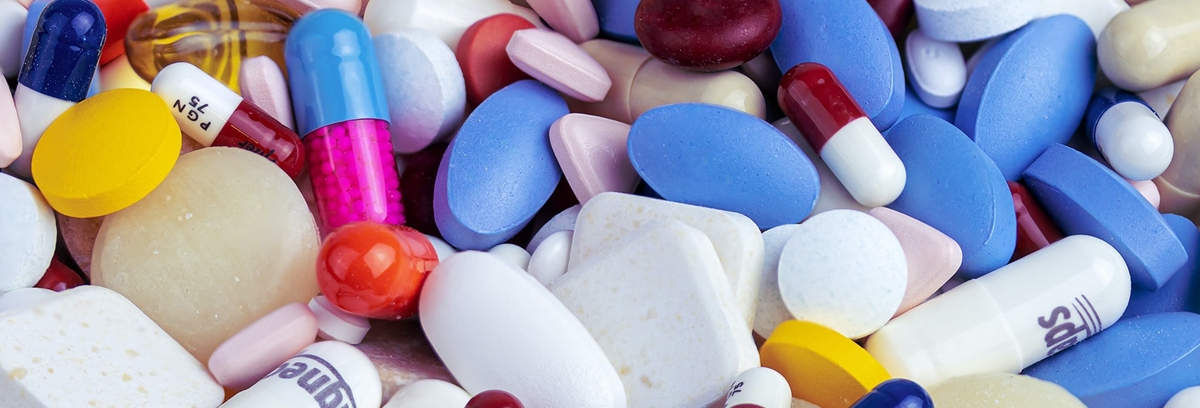
Additionally, the product needs to come with clear and understandable instructions which comply with Good Documentation Practices, deprived of ambiguous or confusing language.
Also, operators should be well trained and properly qualified. All processes and production taking place should be documented, either manually or by machines, keeping track of the progress and quality maintenance.
Finally, if a product loses its quality during transportation, receives complaints from customers or meets other problems, it should be re-analyzed and, if necessary, withdrawn from the market.
- Validation was developed as a means of documenting systematic evaluation of the sterilization cycle — building in a safety factor — and identifying the critical parameters that need to be controlled to assure process performance.
- GMP is that part of quality assurance which ensures that products are consistently produced and controlled to the quality standards appropriate to their intended use. GMP is aimed primarily at diminishing the risk inherent in any pharmaceutical production. Such risks are essentially of two types: cross-contamination (in particular, with unexpected contaminants) and mix-ups (for example, false labeling).
- Documentation is the key to GMP compliance and ensures traceability of all development, manufacturing, and testing activities. Documentation provides the route for auditors to assess the overall quality of operations within a company and the final product.
- Requirements for specific documents or record, including ownership, content, authorization, and change control procedures, has to be described or cross-referenced in the quality modules which relate to the subject of the document.
- Documents must be regularly reviewed and kept up-to-date. When a document has been revised, systems must be operated to prevent inadvertent use of superseded documents (e.g., only current documentation should be available for use).
- The manufacturer should prepare a succinct document in the form of a ‘Site Master File,’ containing specific and factual GMP about the production and/or control of pharmaceutical manufacturing procedures carried out at the premises.
- Laboratory control records should include complete data derived from all tests conducted to ensure compliance with established specifications and standards, including examinations and assays.
Why Is GMP Training Crucial?
The importance of GMP is quite self-explanatory. Basically, following GMP requirements is a proper way of producing high quality goods that will not fail to deliver the desired effect or serve a predefined purpose, helping the customers find what they are looking for. So, every company which deals with the above mentioned aspects of production should have a trained GMP member of the staff, making sure that all the regulations and rules are met.
Producing low-quality products which do not meet the necessary standards will prove to be nothing more than a mere waste of funds and production of materials. Thus, each company should concentrate on producing solely high-quality goods, keeping the consumers safe and satisfied.
Moreover, companies with low-quality products are likely to have their export options reduced. However, GMP training allows the staff to understand and realize the potential behind creating high-quality products, matching the export requirements with ease.
Finally, consumers are more likely to purchase products that have a reputation of being of good quality. This ensures sales and keeps the producer in the business. Product recalls can lead to bankruptcy and this is certainly not in any company's plan. Thus, invest in good GMP training and it will reflect on your company more than beneficially, increasing your export choices, the number of customers, and, above all, the quality of your products.
Your thoughts on this
Loading...